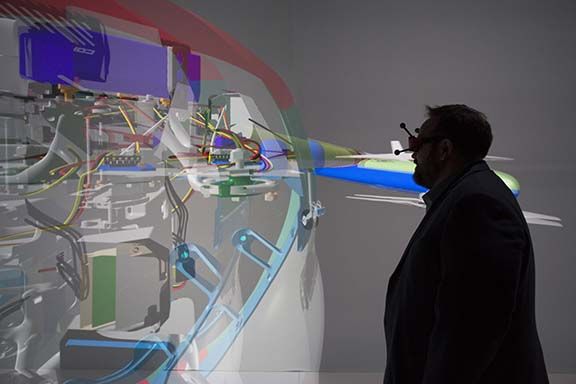
In a virtual reality lab, engineers are testing materials and digital prototypes before they enter the physical world. This is allowing them to work out problems and test earlier in product development and to take products to market faster and more efficiently. A recent survey by PwC found that more than one-third of U.S. manufacturers are already using VR in some capacity or are planning to do so in the next three years.
The new 3D Experience Center at the Innovation Campus at Wichita State University in Wichita, Kansas, aims to advance virtual product development. The center, which opened last month and is a partnership between Wichita State’s National Institute for Aviation Research (NIAR) and French software company Dassault Systèmes, brings together researchers, students and industry to enable 3D advanced product development, virtual simulation and next-generation manufacturing. Aeronautics manufacturer Airbus has signed on as the first tenant on the campus.
Michel Tellier, vice president of Aerospace and Defense Industry at Dassault Systèmes, said that the center will help manufacturers solve many of today’s problems while also training the workforce for tomorrow. The facilities will be open to any manufacturer and will offer the opportunity to create digital models and test them in the 3D cave.
“more than one-third of U.S. manufacturers are already using VR in some capacity or are planning to do so in the next three years.”
Once they have an optimized model, they will then be able to print and further test 3D models in a variety of materials. Tellier said the center offers all physical assets for testing, certification and validation. He calls it an “industrial-grade cubicle” where manufacturers can come and experiment with next-generation practices and processes in an efficient way.
“You can fabricate all the test components you need and then push those all into the labs and have them verified, as well…Technically speaking, you wouldn’t even have to physically come here to do it,” Tellier said.
A number of other university research sites are combining CAD-based additive manufacturing with 3D capabilities, as well. Purdue University, for instance, recently received a grant to pursue VR-based training for manufacturing technologists. The University of Sheffield’s Advanced Manufacturing Research Centre in England is also using VR and robotics to test how manufacturers can make designs more efficient.
Sheffield’s virtual product development will enable the testing of new materials and the ability to engage in multiscale simulation and optimization. To fully test the concept of using the center as a design-to-market facility, researchers from NIAR and Dassault Systèmes created a drone from scratch by testing models in the VR cave and then making 3D printed parts on site.
Airplane manufacturer Airbus recently signed on with the project and moved its Airbus Americas Wichita Engineering Center to the innovation campus at the beginning of the year. Three hundred Airbus employees are currently working on designs for the Airbus A350 XWB aircraft, which relies heavily on 3D printed parts, including 3D printed nozzles and more than 1,000 plastic parts.
The Innovation Campus is situated on 130 acres with abundant space for expansion, Tellier said. Wichita State University is working to recruit other tenants to the center and develop it into a national hub for advanced manufacturing design. “We don’t want to restrict this to aerospace. What we are doing here will bring value to other companies that want to understand how products are going to be innovated, created and regulated,” Tellier said.